Plastic is the nemesis of our time, clogging the oceans and strangling the land. Carina Bailey takes a look at what the moving and packaging industries are doing to help combat the problem
The world is drowning in plastic. The UN Environment Programme thinks that plastics make up as much as 95 per cent of the marine litter found on coastlines, sea surface and the ocean floor, while various reports have estimated that the amount of plastic finding its way into our oceans worldwide is anywhere between 4.8 and 12.7 million tonnes each year.
Others have claimed that, since the Second World War, humans have made enough plastic to coat the entire planet in clingfilm, while the plastic being dumped in our oceans is apparently the equivalent of one refuse truck’s-worth every minute – and rising.
It’s unclear how much the moving industry contributes to the problem but, according to the more ecologically minded packaging companies, there needs to be a radical shift within some global relocation companies to look at their corporate social responsibilities – not just the financial cost of using environmentally friendly packing products – if we are to help loosen the grip of plastic on our planet.
Doing the right thing
UK-based KES Packaging manufactures paper packaging products used for household goods during transit. According to Managing Director Kirk Smith, the company’s aim is to use recyclable products in-house, as well as through its clients. ‘I hate selling plastic, non-recyclable packaging, but that’s sometimes what our customers demand,’ says Smith.
One of the ways the moving industry contributes to the plastics problem is through the use of plastic laminate bubble wrap. Smith explains: ‘Although this carries a recyclable logo, it is only recyclable if the three components are separated. This is time-consuming and costly – therefore, the product will be used once and go directly to landfill.
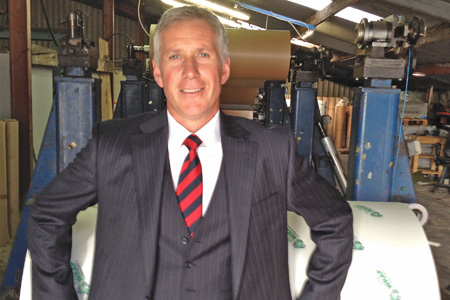
‘The problem I see is that an overseas company will use it and the company receiving this and unpacking then has to pay landfill charges to dispose of it. I know that it is easier to wrap with, it will require less time and certainly less skill to wrap with this plastic product but, the claims for damage are higher and the art of wrapping is being lost from the industry.’
Over the past five years, the increased cost of paper has been an issue. According to articles in the paper industry press, growing demand, caused by a rise in e-commerce, shelf-ready packaging and the public’s declining appetite for plastic – coupled with a shortage of supply – created the perfect storm for hiking prices.
Smith adds: ‘Paper costs have risen so much in the past five years – and there has been a shortage of paper for the past two or three years – meaning plastic may have a price advantage over paper initially for the company wrapping the household effects, but the disposal of this is passed onto the company doing the unpacking.’
There are options available, such as paper blankets, paper mattress covers and paper sofa covers but, according to Smith, there’s little motivation for moving companies to turn ‘green’.
He says: ‘It all comes down to money. There is no incentive for major removals companies to do their bit because they get no benefit – possibly apart from kudos – in using recyclable products.
‘They pack the items, deliver the consignment and it is then the duty of the receiving company to dispose of the packing waste.’
He adds: ‘There is a difference between doing things right and doing the right things.’
KES, based in Slough, has been using eco-friendly products for years within its sector and developed a five-ply paper product – Planetwrap – to closely resemble the plastic bubble laminate commonly used throughout the world, which is made from recyclable paper. ‘Thankfully,’ says Smith, ‘paper and eco-friendly products are still being used by the top-end global corporations.’
The benefits of using eco-friendly products are that most are breathable – preventing moisture build-up – and shower proof. The products are easily recyclable in any country and do not need to go to landfill, although Smith admits that some eco-friendly products may take slightly longer to wrap items and require more skill to fit.
Speaking about Planetwrap, he says: ‘If only the big removal companies would get behind products like this… the change has to start somewhere. Maybe this could be client-led, applying pressure on eco grounds, rather than pricing. Remember, too, that this product will deliver a revenue at the end of its life by being recycled, rather than going to landfill and costing money.’
So, what does Smith think the future holds for the packaging market? ‘Until people’s way of thinking changes, the industry will be putting millions of cubic metres of plastic into landfill rather than recycling across the world. Just as High Street shoppers are ditching the plastic bag for reusable ones, changes need to be made and momentum gathered. Government and industry collaboration and intervention is vital for change to come.
‘As for KES, these are exciting times. The production side of the business is under new ownership, but I will be involved daily in a consultancy role to effect a smooth transition. The new owners are mill agents and paper convertors, which gives them an advantage on obtaining supply and continuity and controls costs, because of the working relationship with the mills.’
Asian Tigers Mobility – a different perspective
One large moving company that has been ahead of the environmental curve for about 20 years is Asian Tigers Mobility (ATM), which was the first moving company in the world to be awarded ISO 14001 Environmental Management System Certification (see page 63 for more on its general environmental achievements).
In terms of its packaging endeavours, the company uses reusable ‘bubble-pack’ bags in packing wherever possible – for example, when packing kitchenware, crystal-ware, silverware and fine china, to reduce the use of tissues/newsprints and brown wax papers. It also reuses cartons salvaged from inbound shipments for domestic removals, and reuses wood salvaged from inbound shipments to make crates.
According to Chairman Gordon Bell, it continues to innovate and improve its packaging to ensure environmentally friendly products, safety and durability. Specifically for its domestic moves, the company has developed – and uses – reusable plastic bins/containers and cooler boxes to replace carton boxes, and has invested in furniture blankets to protect bulky pieces of furniture during a move.
Bell says: ‘By using fully reusable unique “Strong Wrap”, plastic containers and cooler boxes, as well as recycled cartons for home and furnishings, we constantly give customers’ possessions the safest handling and protection.
‘We also moved away from wooden pallets meant for international air shipments, and substituted them with recyclable cardboard pallets, which have proved to be stronger, lighter and more environmentally friendly.
‘Corrugated paper pallets – made from recycled papers – are used to substitute wooden pallets as an alternative for air-palletising operations to achieve zero waste disposal and generate recycling revenue.’
‘Corrugation is the future’
Sofrapack was launched 13 years ago by Guillaume Rochman, who is now the company’s General Manager. At the time, the ISPM15* international standard for solid wood packaging was introduced for imports into Europe from outside the EU, with the company’s goal to supply good quality and green packaging solutions to movers. Rochman says: ‘The future is in corrugated and recycled paper, absolutely not wood and plastic.’
Rochman adds: ‘I wanted to give possibilities to movers to get strong and high-quality products with other kinds of innovative green-packaging solutions, such as corrugated crates and, later (last year), the PleatWrap. Most French movers, and a large number of other European movers, use our products because they are strong, light, ISPM15-free and green for the environment.’
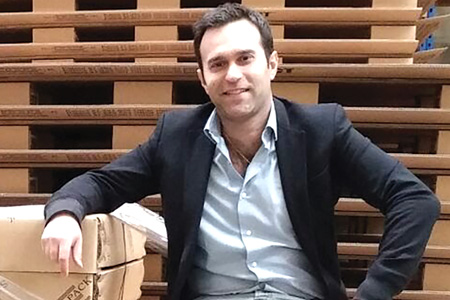
‘ISPM15 treatment is chemical… and you need to pay to get rid of wood, whereas the corrugated – used correctly – is green and free to destroy.’
Sofrapack manufactures strong corrugated custom crates to replace wooden ones, and strong paper wrap – PleatWrap – to replace any pad or bubble wrap, saying they’re much greener than using wood or plastic.
It has taken time, but Rochman can see a change in movers’ attitude to the environment. He explains: ‘It’s hard to change the habits of movers.
‘In the past, movers only wanted wood because customers wanted it, thinking wood is strong and there is nothing to replace it that can offer the same protection and safety during transport.
‘With time, Sofrapack proved to movers that corrugated crates are the solution. We educated customers, telling them that we use good packaging products that are strong, corrugated and much greener.’
Rochman says Sofrapack’s products are high quality, which their price reflects, and claims alternatives are still 30 per cent cheaper than using wooden crates.
According to Rochman, the challenge in making eco products is to design good packaging products that answer all the requirements a mover has. He adds: ‘Making green corrugated crates is easy, but making strong and useful ones is something else.
‘When we decided to make corrugated crates, we tried to anticipate all needs of the removal companies – they had to be strong, easy to work with and cheaper. We met all three points.
‘It is also benefits movers to use Sofrapack green-packaging solutions because it helps them to meet ISO standards.’
Rochman says the company’s next challenge is to try to convince all movers that saving the planet is the job of everyone, and using Sofrapack’s green-packaging solutions is a start.
*The ISPM15 standard describes the phytosanitary measures that reduce the risk of introducing and spreading pests associated with the movement of wood-packaging material made from raw wood in international trade. Wood-packaging material covered by this standard includes dunnage, but excludes wood packaging made from wood processed in such a way that it is free from pests – for example, plywood.
Bin2Barrel to revolutionise plastic waste
In the Port of Amsterdam, a new factory is being built that could revolutionise the way plastic waste is disposed of. With groundbreaking technology, the facility will use previously unrecyclable plastic to create fuel for diesel-powered cargo ships.
The group behind the facility is Bin2Barrel, a Dutch company founded in 2012 by waste management entrepreneurs Floris Geeris and Paul Harkema. While the chemical-recycling technology used in the past has worked, Bin2Barrel is the first company to use it commercially.
If all goes well, this will be the first of four such ‘plastic-to-fuel’ factories to be built near the port. In the initial year, it’s estimated that 35,000 tonnes of rubbish will be converted into 30 million litres of fuel, giving value to materials that would otherwise go to waste, and an estimated annual reduction in CO2 emissions of 57,000 tonnes.
Sofrapack’s products
All of Sofrapack’s products come with worldwide patents. Among its products are:
- Specific crates for pianos, motorcycles, paintings and chandeliers
- Liftvans that use strong corrugated pallets
- Air freight crates
- All of its products can come with unique corrugated pallets, which are handmade.