FIDI Affiliates in Namibia, South Africa, Zambia and Zimbabwe are investing in business initiatives that will help protect the environmental riches of both the region and the wider world. They are also making people-focused changes that demonstrate the benefits of taking a broad approach to sustainability that includes social change. Andrew Mourant reports
Freak heatwaves in Canada; devastating floods in Belgium and Germany. Different phenomena in regions half a world apart, but scientists believe climate change is the common factor between these extremes. A reminder, perhaps, that switching to LED lighting in a South African removals warehouse, although a small thing in itself, matters in the grand scheme of things.
It epitomises a culture change that’s taken root among FIDI Affiliates. However, going green is a long-term commitment, often a challenge, and just one among many they have to face. When FIDI Focus contacted companies in Southern Africa they had a lot else on their plate. Some were – literally – fighting fires, the fallout from civil unrest.
Removals is an industry used to being stress-tested, however, and one that could give lessons in resourcefulness and durability. Stuttaford Van Lines, a dominant presence on the scene, has ridden many a storm during its 163-year history. It has a network of 14 branches and sales offices, and a fleet of around 600 vehicles. Trade covers large local, national and international relocations. Its scope ranges from huge corporate relocations, involving 800 families at a time, to moving rare antiques.
So, the scale of its switch to green practices is significant, symbolically and practically. ‘The biggest challenge has been changing all our vehicles to Euro 3 engines,’ says director Charl Pienaar. ‘These use lower-sulphur diesel. That results in lower emissions from our Mercedes-Benz and Fuso trucks – “our green billboards”. ‘It all took time, with vehicles replaced depending on age and wear and tear. Euro 3 engines work best with the diesel we have available in South Africa. Although Euro 5 is already available, it’s not yet a viable option here. Our suppliers are, however, in discussions to enable us to make the change in future.’
Stuttaford trucks have vehicle-management devices to control speeds and driver behaviour, to help cut emissions on long and short trips. ‘Teams who book the moves ensure they send the most economically friendly truck, based on the volume of goods,’ says Pienaar.
Other green initiatives across the group include widespread use of solar panels at company buildings, tanks to store water for washing vehicles, and buying paper and printing accessories made of recycled materials. Shredded paper is recycled, as are waste oil and scrap parts, collected by outside companies.
Staff on sustainability
FIDI Affiliates are usually open to ideas from staff about green measures and Stuttaford is no exception. One employee devised a scheme to reduce timber usage. The outcome is that Stuttaford now equips vehicles with a crate to accommodate various size pictures/paintings – each wrapped artwork can be housed in individual slots within the crate.
‘Suppliers of tyres, paint, pack material, and so on also share green technologies with us,’ Pienaar says. ‘If it’s something we can use in day-to-day operations, we look at the costs and implications.’ The company has bi-annual meetings to share the latest equipment/materials and ideas. ‘Our biggest drive currently is to limit the use of plastic.’
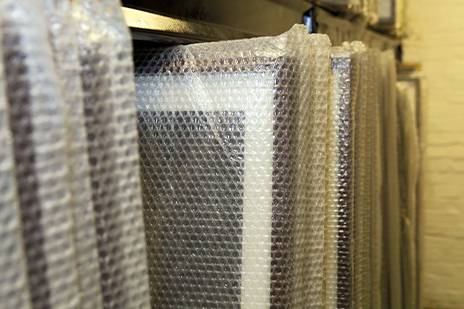
A positive knock-on from the COVID-19 pandemic is that it ‘forced the company to relook at things holistically’. Packing and travel routes are better planned to ensure drivers stay safe, space within trucks better used, and staff and drivers rotated. Virtual surveys became ‘a massive thing’ in South Africa when COVID hit, says Pienaar. ‘From April to May 2020, we had limited staff at the offices – only those who absolutely had to be there, mainly to ensure payments were made and that people had the support they needed. COVID became the catalyst in encouraging our branches to become paperless.’
Stuttaford expects business partners to show evidence of cutting their carbon footprint. ‘Our main supplier of packaging materials remakes these from used ones we send back,’ says Pienaar. ‘We also encourage clients to let us pack for them when moving – we have this down to a science.’
People-focused policy
Aside from any environmentally conscious changes, one sign of a healthy company is the way it treats its staff. Stuttaford annually reviews policies relating to employment equity, sustainability and job security wherever it has branches. ‘Salaries have been reviewed in the provinces, as well as in Namibia, Lesotho and Eswatini (formerly Swaziland),’ says Pienaar. ‘These were adjusted to ensure our minimum wage is more than what’s offered locally.
‘We paid a monthly advance for April to May 2020, when South Africa was at its highest lockdown level. This was to ensure staff could continue to put food on their tables, as well as have money to access medical assistance if required.
‘Our main focus in this pandemic is letting staff know they’re part of a community. We’ve adjusted things to ensure we have the best people for the jobs at hand, ensuring their safety at all times. Our HR team attends seminars and webinars run by our medical aid partner, to ensure our equipment is in accordance with helping fight the virus.’
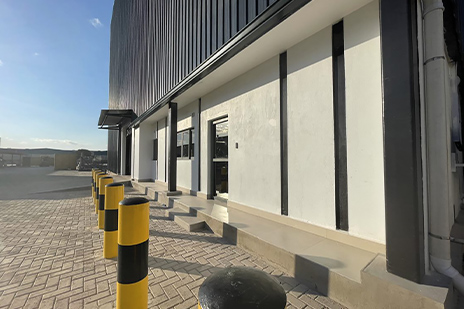
Much of what Stuttaford has done is echoed in AGS Zambia’s operations. Having upgraded its fleet of smaller vehicles, it’s now doing the same with trucks. ‘This will allow our transport to be as environmentally friendly as possible,’ says managing director Chaka Buhendwa.
There’s been a big drive at AGS to improve packaging, making changes to ensure recyclable materials are used and buying new cartons that don’t require bleaching. ‘We’re providing reusable plastic boxes and blanket wrapping as an alternative to cardboard, which we retrieve after delivery for reuse,’ says Buhendwa. ‘This drastically reduces the amount of packaging material we use, and cuts costs for the client.’
That may sound simple enough, but, adds Buhendwa, making that change without compromising service standards proved a challenge, not least in persuading clients of the benefits.
Like Stuttaford, AGS expects its transportation partners to prove their green credentials. ‘When we review our choice of shipping lines, hauliers or air carriers, we give extra consideration to those willing to change their habits for the better.’
COVID, Buhendwa adds, has ‘completely changed our view of how our activities should be conducted, and allowed us to rethink move processes.’ That means many more virtual surveys, reduced vehicle use, and some staff walking to work. ‘The pandemic prompted us to find alternatives to a physical presence at the office without jeopardising the human interaction needed for proper communication and follow up.’
AGS is, he says, committed to developing employee capability through its training programmes. ‘In 2020, we spent ¤440,000 at group level on technical, administrative, sales and management coaching – the equivalent of 20,000 training hours.
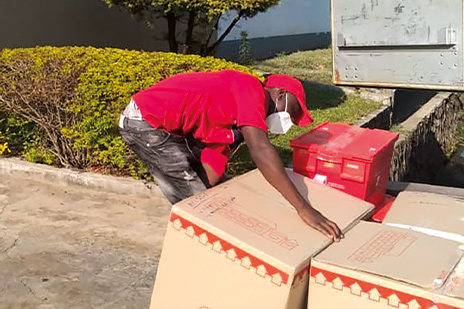
‘And although mobility relies heavily on male workers, because the job requires physical strength, 39 per cent of our staff were female in 2020 – an improvement of 16 per cent since 2016, when we first implemented the UN women’s empowerment principles. Moreover, when selecting suppliers, we use non-discriminatory criteria to ensure female-owned companies are given fair opportunity.’
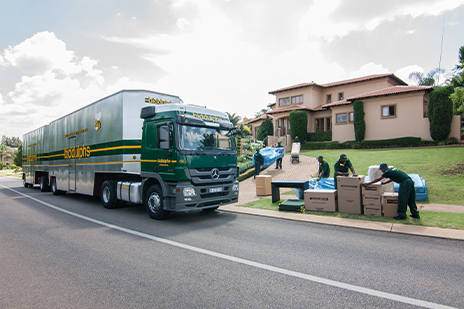
Green initiatives
Biddulphs International is another enduring presence in Southern Africa’s removals landscape. A fourth-generation family-owned business, founded in Zimbabwe in 1928, it has grown into the region’s largest independent removals company. It has around 180 vehicles and employs more than 800 staff across 15 branches throughout South Africa, Zimbabwe and Botswana. It handles large and small international, domestic and commercial relocations.
Biddulphs takes green initiatives seriously – so much so that it has established a separate company, run by one of its former drivers, focused on recycling more than 120,000kg of cardboard, paper and plastics every year. ‘We aim to continue growing this side of the business and to explore other sustainable measures,’ says chief operations officer Ryan Gibbons.
Employees contribute significantly to this drive. Shop-floor initiatives are behind the widespread adaptation of warehouse roofing to accommodate solar panels, a source of energy that the country has spurned for far too long, Gibbons believes. ‘South Africa has an average of 2,500 hours of sun every year, which isn’t used effectively by business or the nation.’
Simple steps and social change
Like Stuttaford and AGS, Biddulphs has embraced ‘simple initiatives that can go a long way and make a big difference’ – such as educating employees to print on both sides of a piece of paper. More ambitiously, the firm has retrofitted depots with 5,000- and 10,000-litre tanks, to store rainwater that collects in guttering.
‘In some, we can store 50,000 to 100,000 litres, and use it to wash vehicles or supply water when needed in dry months,’ says Gibbons.
The company has spent heavily on new trucks – several new Mercedes Benz Actros 1842s models direct from Germany, with engine technology designed to cut emissions and reduce fuel consumption. A new long-distance combination with trailers can cost upwards of US$250,000. ‘We’re investing in ergonomic lightweight designs to make our trailers more aerodynamic, and selecting tyres for maximum longevity. We reduce our carbon footprint by having fewer road trips and more volume,’ says Gibbons.
COVID has left Biddulphs with much to ponder. The pandemic is estimated to have reduced South Africa’s daily carbon emissions by nearly 20 per cent as the economy shrank. One legacy is that the firm has shown ‘a lot more flexibility’ towards employees working from home, post-lockdown.
Biddulphs has, says Gibbons, embraced social change in South Africa in line with government Black Economic Empowerment requirements. The firm has revised employee policies on violence, harassment and discrimination ‘to ensure our employees are aware of where they can get help, and from whom, if needs be. Our industry has yearly targets and goals to improve workforce gender and designated group imbalances.’
He agrees that the removals industry is characterised by long hours and heavy lifting, and ‘stereotypically’ filled by men. However, over the past six years, Biddulphs has increased its number of women employees by 120 per cent. ‘We aim to continue with this,’ Gibbons says. ‘Moreover, nearly six per cent of our employees in South Africa have a disability – we’re leaders in recruiting the disabled. More than 90 per cent of our middle-management team are from “previously disadvantaged designated groups”. We’re constantly planning a better future for employees in how we carry out recruitment and succession.’
Turmoil on the streets: Ryan Gibbons’ frontline view
‘As a business that’s been in operation for more than 93 years, we tend to think we’ve seen it all. However, unprecedented civil insurrection, mainly in the Kwazulu-Natal region, caused disruption to some of our countrywide operations.
‘On 12 July, our Pietermaritzburg branch was looted and burned to the ground – including our main warehouse with all our pallets, self-storage units, a fully stocked workshop, change rooms, three trucks, as well as some of our drivers’ cars.
‘The next day, our Durban branch was also badly looted and vandalised – our main office, warehouse and more than 10 vehicles damaged. The devastation took a toll on hundreds, if not thousands of individuals, businesses and companies alike. It resulted in us flying down special security to take control of our sites again so we could begin rebuilding and retooling.
‘Thankfully, no employees were hurt. Our thoughts go out to clients who suffered some form of loss to their prized possessions. Fortunately, our company has robust insurance cover, besides a comprehensive infrastructure and disaster-management plan.
‘Two days after the events, assessors evaluated the damage. We’d already sent trucks and teams with IT equipment and vehicle spares to get operations back up and running. Our employees helped to clean up our branches where they could, and we’re happy to report that, a week later, we were moving people again.’